Optical processing machine "Lasermeister"
"Lasermeister" is Nikon's proprietary laser processing machine that uses the optical measurement and precision control technologies that Nikon has accumulated with semiconductor lithography systems. It enables various laser processing with high precision. Lasermeister meets a wide range of needs in the field of material processing, including metal additive manufacturing, marking, bonding, and subtractive processing of materials.
Product list
Information on Lasermeister Technology Center
Nikon has a "Lasermeister Technology Center" in its Kumagaya Plant. The Lasermeister Technology Center offers not only opportunities to have a hands-on metal processing experience, but also technical consultation. A reservation is required in advance for the use of the facility.
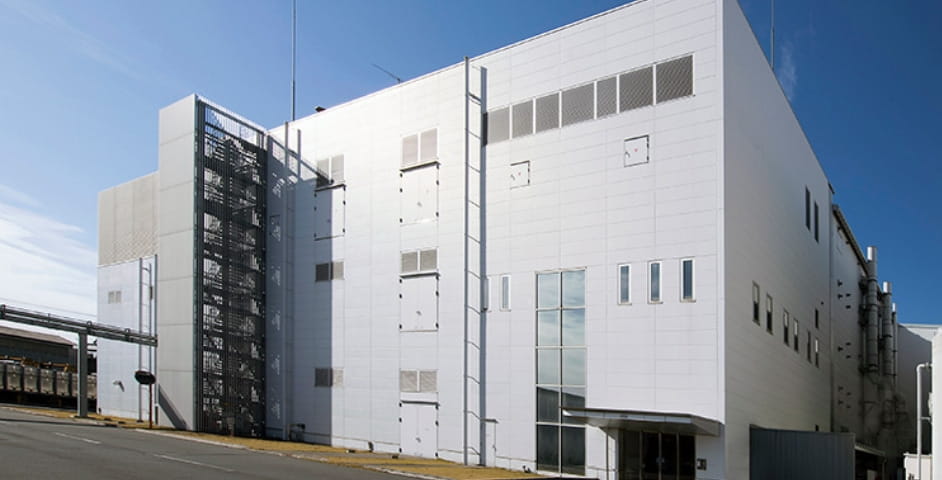
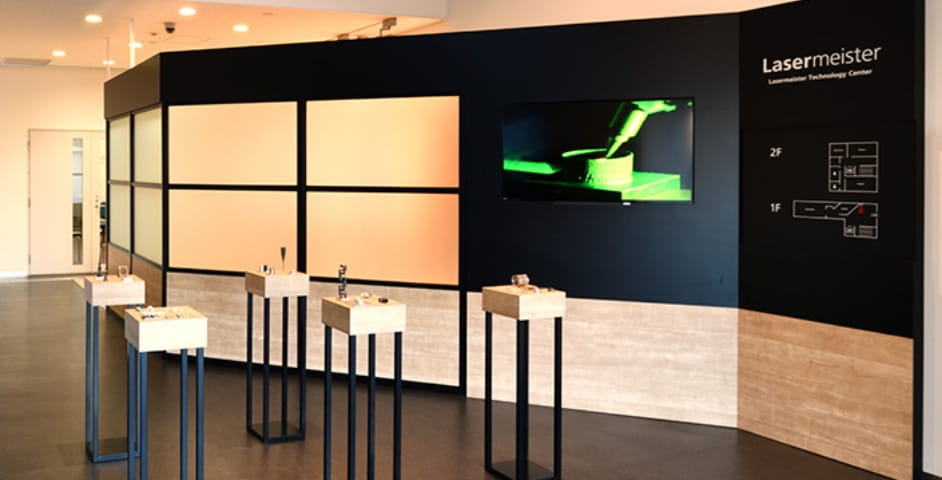
Demonstration Room Information
Address | 201-9 Miizugahara, Kumagaya, Saitama, Japan Inside Kumagaya Plant Kumagaya Plant |
---|---|
Business hours | 10:00–17:00 (every day except Saturdays, Sundays, National Holidays, and Nikon's holiday breaks) |
Reservation | Please fill in the inquiry form. |