Lasermeister 1000Sがもたらす、誰もが簡単に高精度加工を実現できる世界(2)
Lasermeister 1000S
2025.07.17
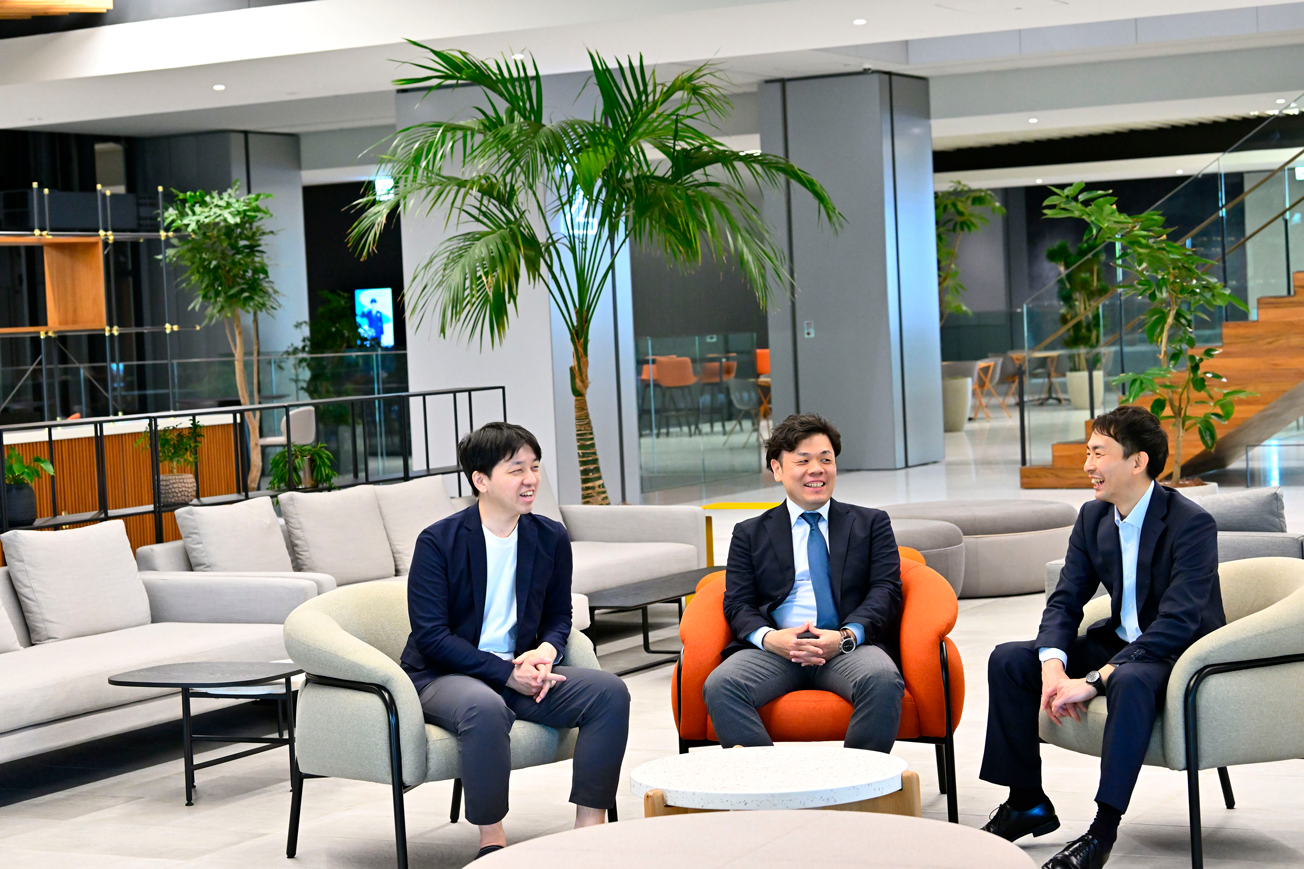
Lasermeister 1000Sは、超短パルスレーザーと機上計測により、高精度・難加工を容易に実現する除去加工機です。除去加工とは、材料の不要な部分を除去して目的の形に加工する方法で、精密金型や半導体装置向け部品加工、その他さまざまな用途で幅広く使われています。一般的な除去加工機は、“熟練者”や“技能者”が手作業で操作するアナログなものですが、Lasermeister 1000Sはデジタルで計測して加工できるのが特長です。ニコンが培ってきた半導体露光装置の技術が数多く活用されたレーザー加工機として、ものづくりを事業とする多くの企業に活用していただくことを目的としています。
企画・営業の藤川貴浩氏、開発に関わった江上茂樹氏、三好誠氏に話を伺いました。
作業者のスキルに依存しない加工を実現
──Lasermeister 1000Sの高精度加工を実現するにあたり、どのような技術コンセプトを基に設計を進めたのでしょうか?
江上:Lasermeister 1000Sは、「Remake Manufacturing(リメイクマニファクチャリング/ものづくりを、つくり変える)」を技術コンセプトに、「高精度加工」を実現しつつ、加工に要していた段取りも不要にする、「段取りレス・スキルレス」も追求した、ニコン独自の加工機として設計しました。
Lasermeister 1000Sの一番の特長は、これまでの加工機にはない、「機上計測」によるオンマシンフィードバック加工を可能にしている点です。加工には超短パルスレーザーを採用しており、非熱のレーザーアブレーション加工を行うことで、材料の熱変形や熱影響を最小限に抑え、金属からセラミックス、ガラスに至るまで、あらゆる材料の加工が1台の装置で可能です。機上計測には光干渉技術を活用した高精度な3D計測機を搭載しており、計測結果をin-situに(その場で)加工にフィードバックするシステムを採用しています。さらに、半導体露光装置由来のキャリブレーション技術も計測と加工システムそれぞれに組み込みました。これらのシステムにより、マイクロ~サブマイクロメートルレベルの高精度な加工を実現し、お客様が求める加工精度が手に入れられる装置になっています。
加えて、光を用いた非接触の計測や加工が可能なため、対象物に直接触れる必要がなく、デジタルにものづくりの加工工程を進めることができます。その結果、従来必要だった複雑な治具設計や煩雑なワーク位置出し、さらにCAMデータの生成といった工程を大幅に簡略化し、作業者のスキルに全く依存しない加工が実現します。
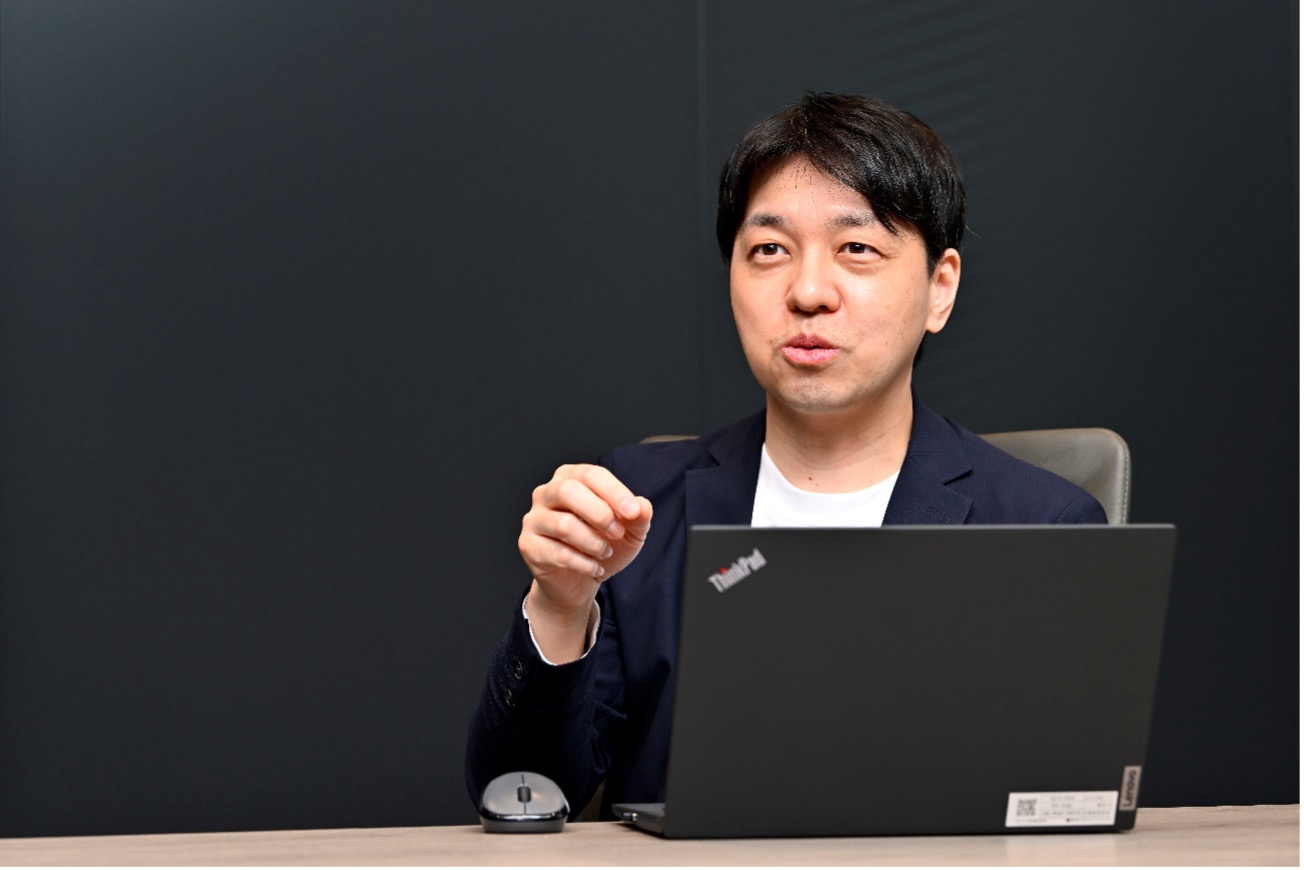
──設計プロセスの課題において、独自のアプローチを採用した部分についてお聞かせください。
江上:Lasermeister 1000Sは、500mm角×高さ180mmのワークを搭載でき、計測・加工ができます。その全域でマイクロメートルオーダーの高精度な加工を実現するのは、非常に難度が高いのですが、ニコン独自の機構設計やキャリブレーション技術を取り入れることでこれを可能にしました。
装置の土台となる定盤やオプティカルベースはグラナイト製の精密石定盤を採用することで、装置全体の剛性を高め、加工や計測時の振動や変形を抑えています。ステージ機構にはワークテーブルを一定の高さで支持できるエアベアリングを採用し、駆動時の摩擦や振動が生じないため、動作が非常にスムーズで安定性が高く、高精度な位置決めを実現できます。また、ニコンの半導体露光装置で培った座標補正技術を活用し、傾斜やスケーリング、直交度などを正確に補正したグローバル座標系を構築しています。これにより、作業者のスキルに依存せず、精度の高い加工を可能にしています。加えて、機上にはレーザービームの出力や位置を検出できる計測機も搭載し、日々の変動を自動的にキャリブレーションする仕組みも備わっています。これらの技術により、広い加工範囲でも安定して高精度な加工を実現しています。
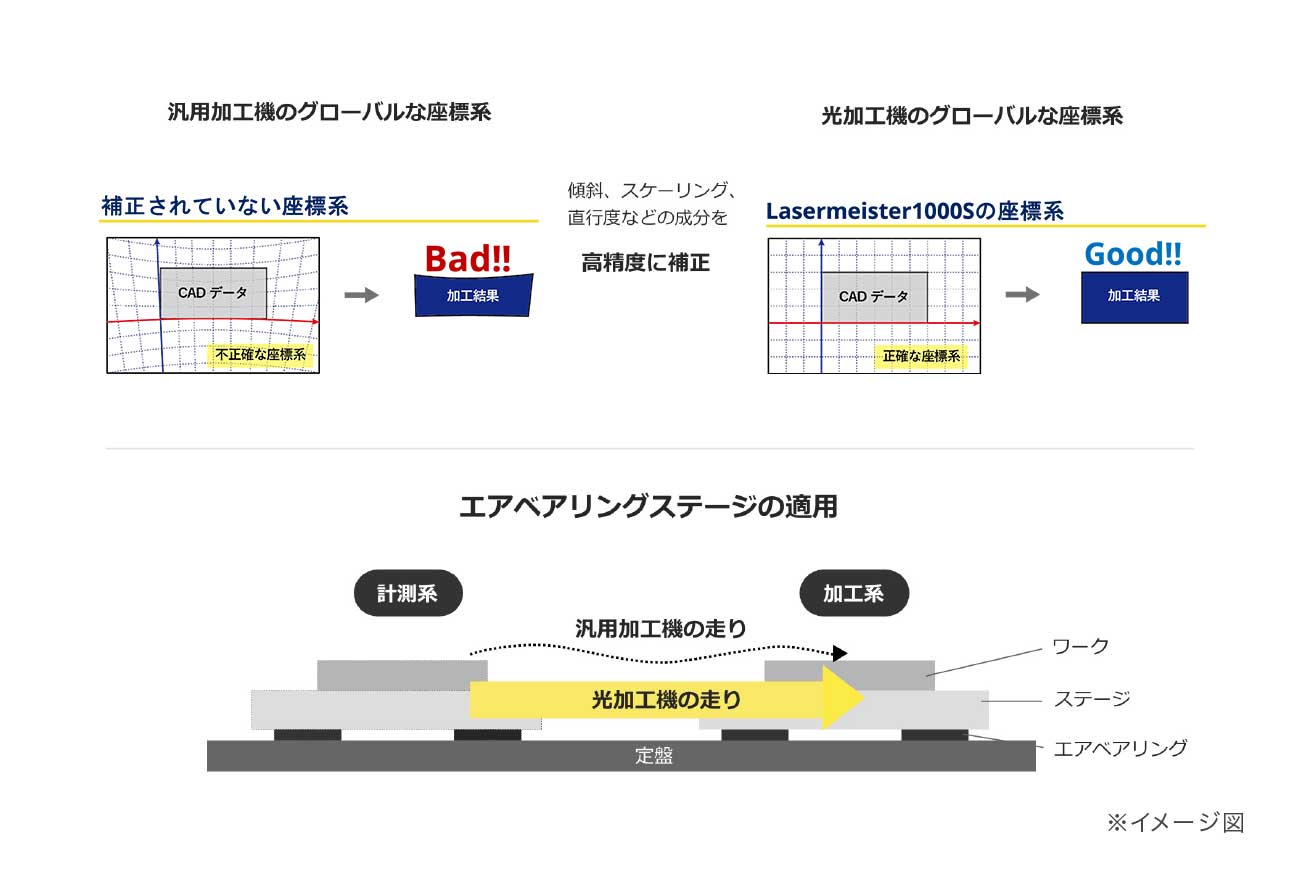
──Lasermeister 1000Sの設計の中で、特に力を入れた技術的なポイントや、他社製品との差別化を意識した工夫について教えていただけますか?
江上:藤川がお話した通り、他社製品との差別化を特に意識したわけではありません。結果、差別化された製品だったということです。そもそも半導体露光装置は、世界でも数社しか作ることができない、技術的に非常に高いものです。その技術を応用しているので、独自の差別化になります。
これまでお話ししたように、Lasermeister 1000Sには超短パルスレーザーや光干渉計測、エアベアリングステージ、さらにキャリブレーション技術といった、先端の技術が1台の加工機に惜しみなく盛り込まれています。ただ、どれだけたくさんの機能や技術を詰め込んだとしても、それが加工機としてしっかり機能し、現場で役に立つものでなければ意味がありません。Lasermeister 1000Sが他と一線を画しているのは、これらの個々の要素や技術を単に寄せ集めるだけでなく、それらを一つの加工機として高いレベルで統合し、全ての技術を最大限に活かせる形に仕上げている点です。言い換えれば、各技術をシステムとして完全にインテグレイト(統合)できる技術力こそが、ニコンの強みであり、Lasermeister 1000Sの真価だと考えています。
また、「誰でも簡単に高精度な加工ができる」というコンセプトを実現するため、高いユーザビリティーも追求しました。そこでは、ソフトウェア開発の担当である三好が尽力してくれました。
──ハードウェアとソフトウェアが密な関係で開発を進められたのですね。
三好:最初の頃は開発メンバーが少数だったため、密に進められました。ミーティングも実験室で装置の前に椅子を並べて、皆で話し合うスタイルでした(笑)。やりやすいサイズ感だったというのはあったと思います。
江上:通常の半導体露光装置の開発とは、そこが全然違いました。小回りを利かして開発ができる。完成された装置ではないので、いろいろな方向性を、その場その場で皆で議論をしながら進めることができました。
──ウォーターフォールではなく、アジャイルで開発されたわけですね。
江上:そうです。ただ、後々、仕様書が整備されていなかったり、更新の抜け漏れがあったりの問題が発生しました。そこは反省点です。
──最も苦労したのは、どういうところでしょうか?
江上:一つは精度課題の対応です。工作機械では一般的な課題ですが、私たちの加工機は広域をミクロンからサブミクロンレベルの精度で加工する必要があります。そのため、加工・計測の安定性やドリフト抑制が重要になります。ただし、全ての部品を高精度に加工したり、組立精度に頼りすぎると、装置価格が高騰し、ユーザーの購買意欲に直接影響してしまいます。そこで、構造材料の選定や装置設計を工夫し、かつ独自のキャリブレーション手法の開発や、熱影響を抑える動作シーケンスの採用により、コストを抑えながら必要な精度を実現することができました。
二つ目は製品化に向けた安全規格や環境適合の対応です。Lasermeister 1000Sは海外販売も視野に入れています。米国や欧州といった海外を仕向地とする場合、装置として適合しなければならない複数の安全規格や、規制物質に対する全ての部品(数千点)のエビデンスが必要になり、これらの調査や設計変更に多くのリソースを要しました。前者の安全規格対応の一例として、我々の加工機はクラス4のレーザーを内蔵しているため、装置外部への光漏れを防ぎ、クラス1機器とするためのチャンバー構造設計に苦心しました。大型装置のため、パネルの公差管理や反り対策が課題となりましたが、シール構造やラビリンス構造を採用し、メンテナンス性を確保しながら、デザイン性との両立も実現することができました。
藤川:Lasermeister 1000Sは、高精度で難しい加工にチャレンジできる装置です。お客様からはさまざまなものを要求されます。それらの要求を達成するためには、緻密に積み上げられた装置設計でなければなりません。江上はそこに厳しい人間でした。お客様に中途半端な装置は出さない、しっかりと作り上げなければならないという話は、よくしていましたし、Lasermeister 1000Sにかける想いや、技術、製品に対する精度へのこだわりは、十分に感じました。
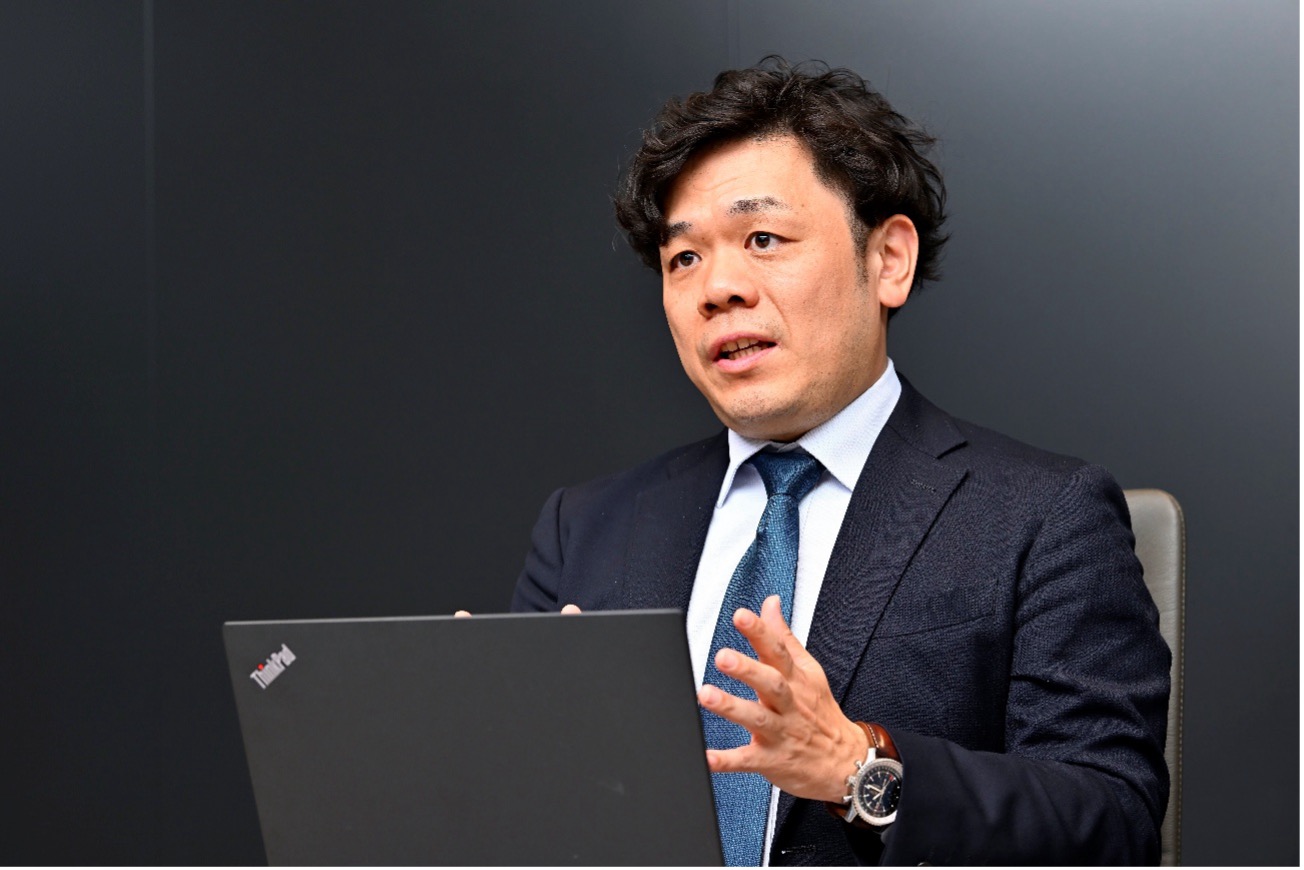
従来の加工機とは一線を画すユーザビリティー
──ソフトウェアの開発、ユーザーインターフェースの設計で、ユーザー体験を向上させるなどの取組みとして、どのような工夫や技術がポイントになりましたか?
三好:江上が言った、「誰でも簡単に高精度な加工ができる」は装置のコンセプトの一つですが、それはソフトウェアが寄与するウエイトが大きくなります。ユーザーが複雑な操作を必要とするようなソフトウェアになっていると、「スキルレスでできる、誰でもできる」とは言えないため、ユーザーにとって使いやすいものを実現できるよう、ソフトウェアのユーザビリティーについては、初期段階から特に注力して開発を進めてきました。
従来の加工機に慣れたユーザーに使いやすいと感じてもらうためには、従来の加工機の操作性に似通ったものがよいという考えもありますが、Lasermeister 1000Sは、機上計測の結果と加工を組み合わせて高精度な加工を実現するというこれまでにない加工機となっているため、従来の加工機のソフトウェアにこだわるのではなく、「Lasermeister 1000Sとして本当に使いやすい形は何か」を意識し、今までにない操作性を作り上げる必要がありました。社内のUIデザイナーや加工機のユーザーなどの有識者と議論を重ねながら開発を進めたことで、従来の加工機とは一線を画す優れたユーザビリティーを実現できたと自信を持っています。具体的には、ユーザーが入力したCADモデルと機上計測機で取得した点群データを重ねて表示する3Dビュー、加工および計測の各ジョブを自由に並べるシーケンス作成画面、加工後の面形状の3D計測結果をその場で簡単に確認できる結果表示画面などを備えています。従来の加工機の操作に慣れている方はもちろん、初めて加工機を使用する方にも、ぜひ一度その操作性を体験していただきたいと思います。
──「誰でも簡単」な装置は、熟練の作業者は敬遠するのではないですか?
三好:そうですね。「誰でも簡単」にするためには、ユーザーの入力が必要なパラメーターの数は少なく、細かな設定パラメーターは内部で自動計算してくれる方がよいです。でも、ユーザーによっては、細かな設定も自分で変更しながら、加工を試したいという要望もあります。そのため、エキスパート用のパラメーター設定画面を用意するなどの工夫をしています。
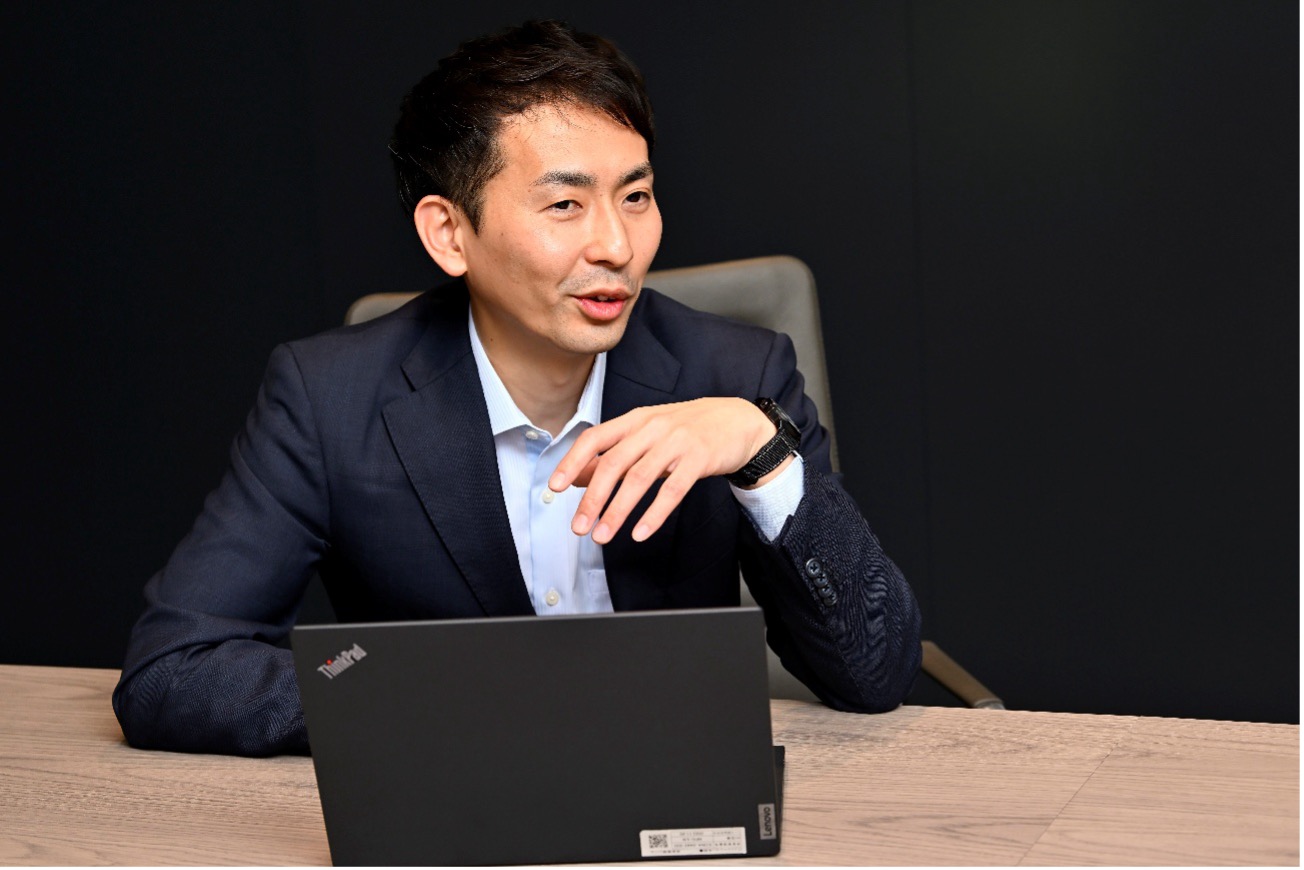
ワーク位置出しとオンマシンCAMの活用
──ワーク位置出し機能について、ユーザーが正確に加工を行うための工夫や技術は何ですか?
三好:Lasermeister 1000Sは、「μm単位の位置精度で加工ができる」とうたっていますが、そのためには、装置のワークテーブル上にワークがどのような位置に、どのような姿勢で置かれているかを、μmレベルで認識する必要があります。それをどう実現するのかが重要でした。
従来の加工機では作業者がワーク位置を測り、測定結果をプログラムに反映するといった段取り作業が必要で、非常に手間がかかります。「段取りレス」をソフトウェアで実現するため、機内に搭載された3D計測機を用いて、ワークの基準面や基準高さを計測し、その計測結果に対して画像処理を行うことで、μm単位の精度で位置出しを行うことを可能としました。ワークを装置に搭載したまま、全ての操作がGUI上で完結するため、作業者による個人差やバラつきが発生することもなく、誰が行っても必ず同じ加工ができます。
──オンマシンCAMの活用により、加工プロセスがどのように効率化されましたか?
三好:従来は、市販のCAMソフトを使用してCADモデルから加工用プログラムを作成し、それを加工機に転送するのが一般的です。しかし、高精度な加工を行うためには、CAM操作が煩雑になることや、CAM操作の熟練者のノウハウが必要になる場合がありました。
Lasermeister 1000Sでは、CADモデルをそのまま装置に転送し、GUI上で加工条件などのパラメーターを設定するだけで、装置のソフトウェアが加工パスを自動生成します。複雑な操作を必要とせず、誰でも簡単に加工の準備が行えるため、事前準備にかかる時間を大幅に短縮できる点は、Lasermeister 1000Sの大きな強みの一つです。
江上:三好には、「システムのコンセプトとして、こうしたいを具現化して欲しい」と常に頼んでいました。オンマシンCAM、つまりCAMレスもその一つでした。CAMレスになったことで、CAMソフトの専門家に頼る必要もなくなりました。
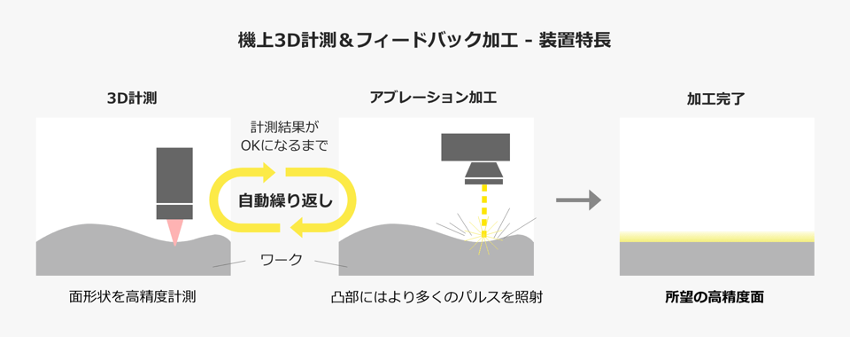
計測フィードバック加工とアドオンの役割
──計測フィードバック加工が、加工の精度や効率にどのような影響を与えていますか?
三好:高精度な加工を実現するためには、加工を途中で止め、装置外の計測機器でワークの表面形状を測定し、その測定結果を加工に反映させることが一般的です。Lasermeister 1000Sでは、内蔵された非接触3D計測機によって測定された結果をソフトウェアが自動的に後続の加工へ反映することができます。これにより、幾何公差サブマイクロメートルレベルの高精度な平面仕上げや微細加工が可能となりました。このプロセスは、GUI上で加工ジョブと計測ジョブをひもづけるという簡単なユーザー操作で実現可能となっており、作業の効率化と高精度な加工を両立しています。
──製品のAdd-on(アドオン)について、ユーザーにとってのメリットや機能としての拡張性を教えてください。
三好:Lasermeister 1000Sは、材質や形状に対する加工の自由度が非常に高く、多様なユースケースに対応可能です。ソフトウェアはできる限り汎用的に使えるよう考慮して開発していますが、お客様の特定のご要望に応じて機能追加が必要となる場合もあります。藤川が精密金型、半導体部品、刃物工具など、さまざまな業界のお客様からご要望を頂いていますが、すると、「追加でこういう機能があると、こんなことができそうだ」というのが見えてきます。そうしたさまざまなニーズに迅速かつ柔軟に対応するため、加工ジョブと計測ジョブから成る一連のシーケンスにアドオンジョブを追加できる仕組みを備えさせました。追加されたアドオンジョブは、シーケンスの一部として自動的に実行されるため、追加処理を実行するためにシーケンスを止める必要はなく、生産性を維持して機能拡張が可能です。例えば、特定の形状検査機能や、特殊なテクスチャー加工の追加といったアドオンが挙げられます。これにより、多様なニーズに柔軟かつ迅速に応えることが可能となっています。
──どういう点に苦労されましたか?
三好:やはり、ユーザーインターフェースのところですね。「この仕様で本当に使いやすいのか」は常に考えていましたし、漠然とした不安をずっと抱えていました。開発途中の段階でお客様に触っていただくのは難しかったので、開発メンバーや、社内で加工機に触れている方にヒアリングやデモをして、使用感を確認しながら進めていました。それでもお客様に実際に触っていただき、「うん、使いやすいね」と言っていただけるまでは、ドキドキしながら作っていました。