Riblet analysis and processing
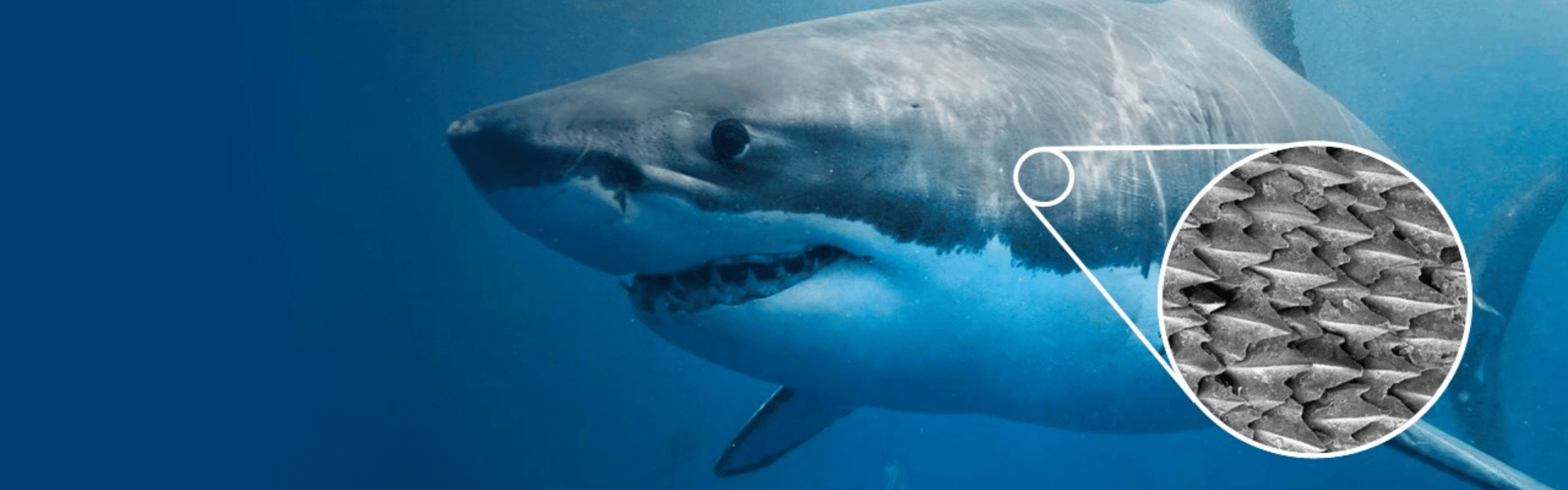
Riblets are said to reduce the frictional resistance of fluids. This section introduces its structure and utility.
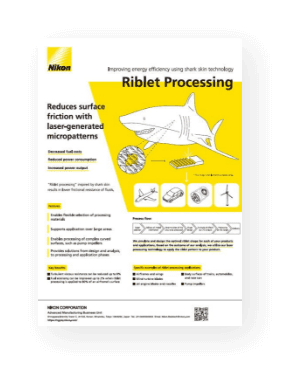
Download some materials related on the riblet
Some research papers on performance evaluation of the riblet and a leaflet about the riblet processing are posted on the download page.
What are riblets?
Riblets are a type of biomimetic technology that has a shark-skin-like pattern structure made artificially. As shown in the photo, the shape is a fine structure consisting of consecutive longitudinal grooves.
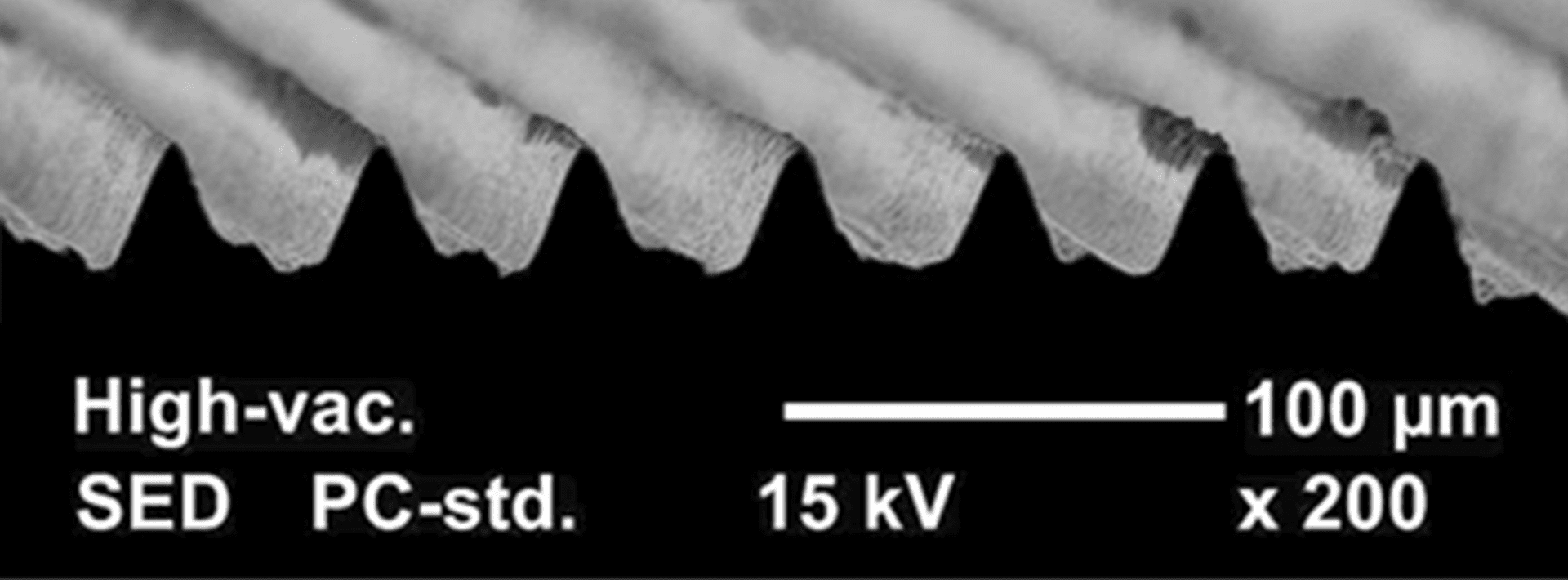
Observed cross-section of riblet processing (SEM image)
Sharks have evolved the surface of their skin to longitudinal groove shape to swim smoothly in the water. This evolution reduces the frictional resistance of contact with the water and makes it possible to swim using less power. Nikon has made it possible to increase energy efficiency by artificially applying riblets, a shark-skin-like pattern structure, to the surface of parts used on various products including gas turbines, jet engines, aircraft and wind turbines.
Mechanism of reducing the frictional resistance of a surface by riblets
The physical phenomenon of riblets is academically widely known.
Resistance in fluids is roughly divided into pressure resistance (inertial resistance) and frictional resistance (viscous resistance), and riblets are effective with respect to frictional resistance.
It is known that strong hairpin vortices are generated in a wall surface boundary layer in the region called the turbulent flow, and the consecutive vertical vortices generated near the wall surface generate frictional resistance.
In addition to their longitudinal grooves creating distance between the vortices and the wall surface, riblets lessen the resistance caused by vortices by reducing the contact area and thus reducing the frictional resistance of contact.
Resistance in fluids is roughly divided into pressure resistance (inertial resistance) and frictional resistance (viscous resistance), and riblets are effective with respect to frictional resistance.
It is known that strong hairpin vortices are generated in a wall surface boundary layer in the region called the turbulent flow, and the consecutive vertical vortices generated near the wall surface generate frictional resistance.
In addition to their longitudinal grooves creating distance between the vortices and the wall surface, riblets lessen the resistance caused by vortices by reducing the contact area and thus reducing the frictional resistance of contact.
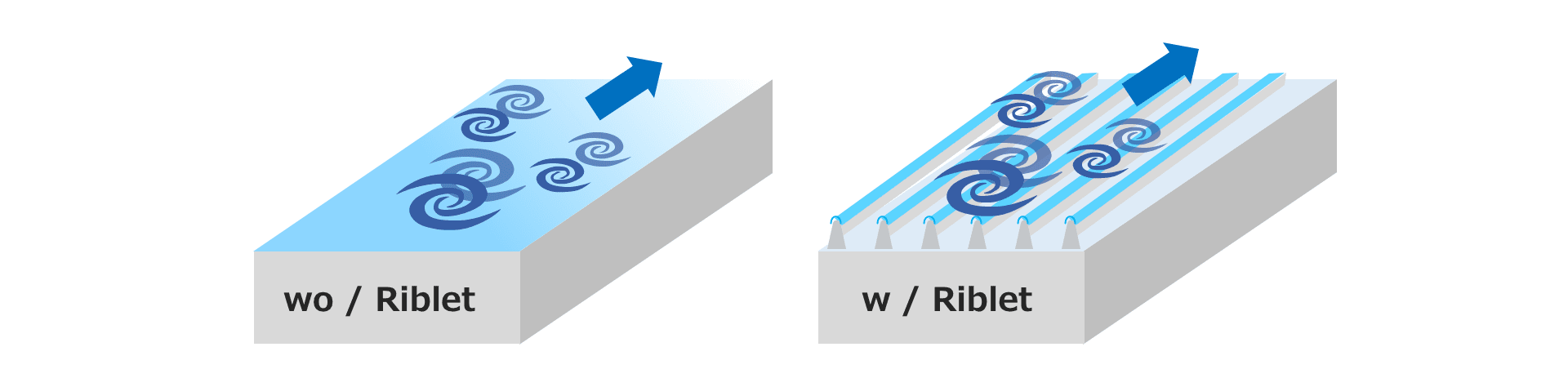
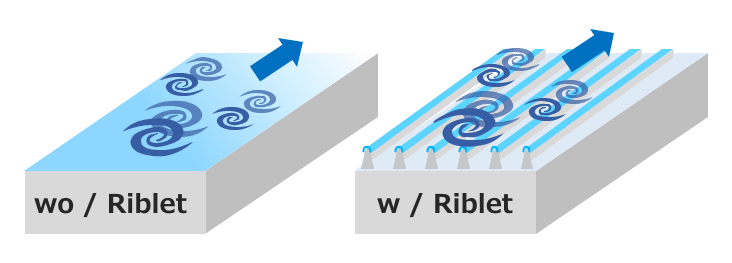
Mechanism of reducing the frictional resistance of a surface by riblets (image)
Originality of Nikon’s riblets
With riblets, the dimensions of the longitudinal grooves differ depending on the wall surface conditions. In other words, in order to maximize the effect, the size and orientation of the longitudinal groove structure must be designed according to the fluid conditions (flow velocity, density, viscosity, flow direction, etc.) at each location where riblets will be applied. The designing of optimal riblet shapes for each part has gradually become possible in recent years due to the development of CFD analysis technology, and Nikon makes the designing of more effective riblets possible by collaborating with bionic surface technologies GmbH, one of the first to specialize in riblet analysis research.

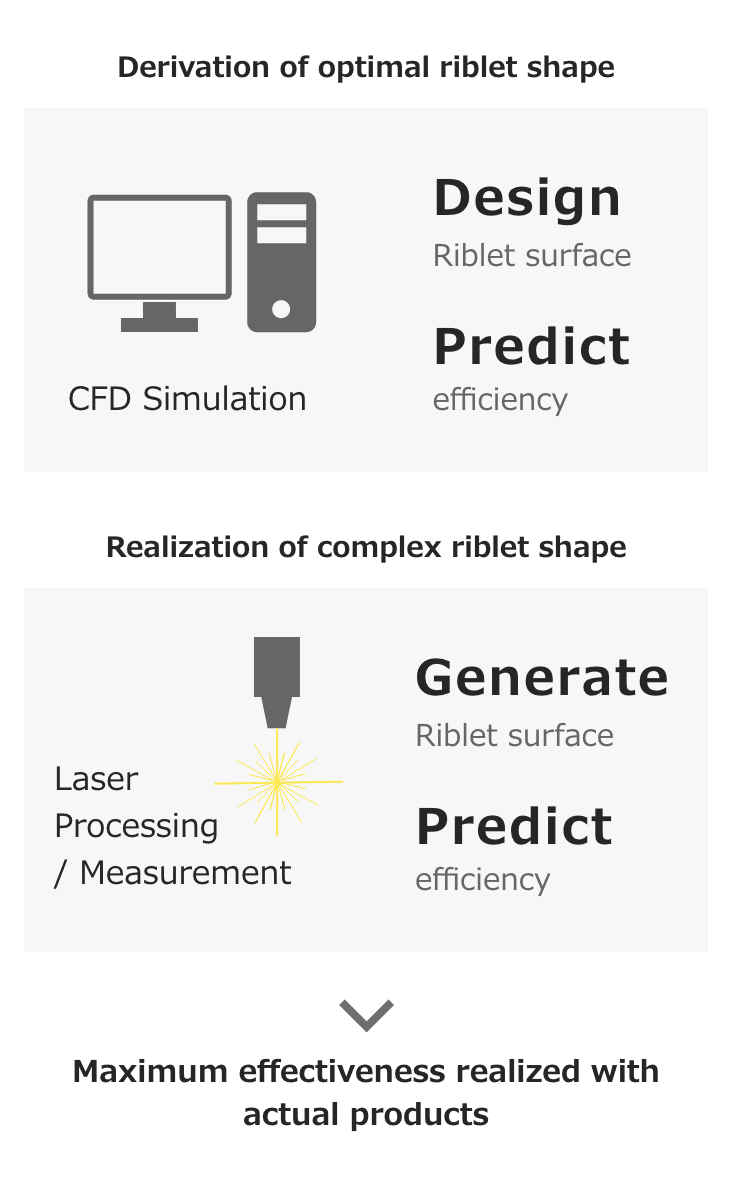
Providing a total service from the optimal design and effect prediction analysis to actual processing
Three flexibilities that Nikon’s riblets bring to the table
As described above, riblets must have the optimal shape and dimensions for each part they are used on. After a design is derived by analysis, it must then be implemented. This was conventionally performed by molding a resin film using a die. However, implementation of optimal riblet design had not yet been realized because it was necessary to create dies with many patterns to implement the optimal riblet shape on each part. Nikon’s riblet processing using a laser brought three flexibilities to the world of riblets, thus removing the limitations that existed previously.
- 1. Flexibility with respect to the material to be processed
- 2. Flexibility with respect to the shape to be created
- 3. Flexibility with respect to riblet design
Flexibility 1: Target material
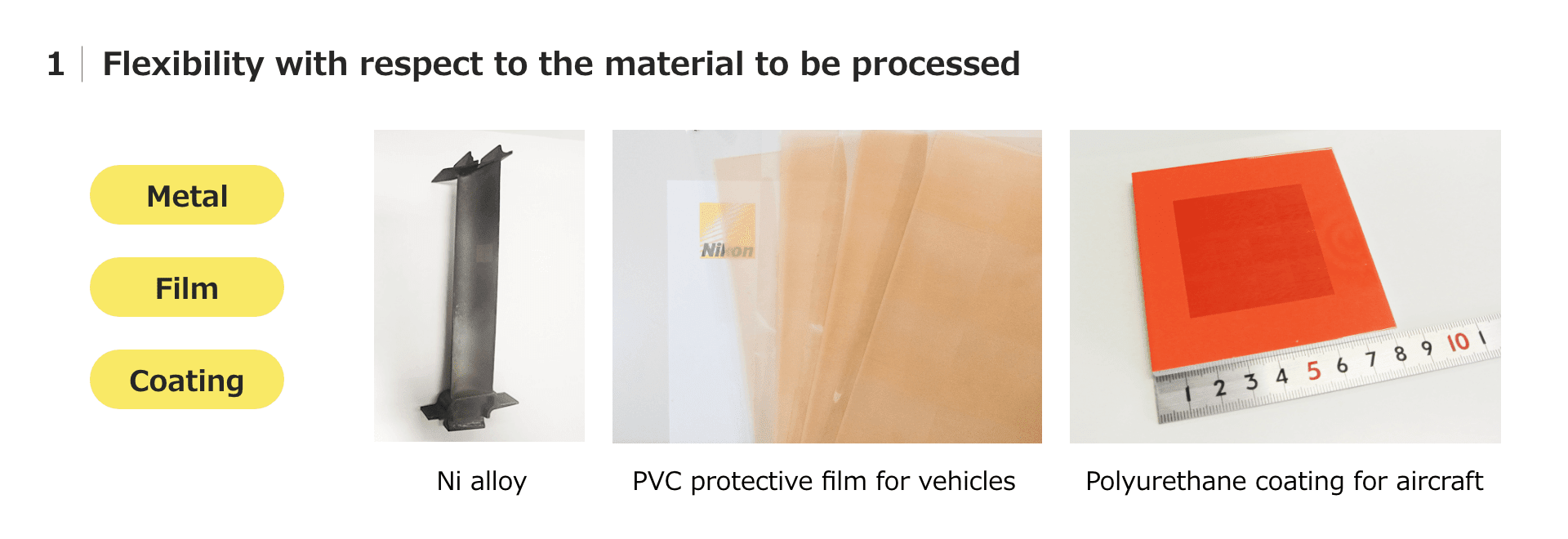
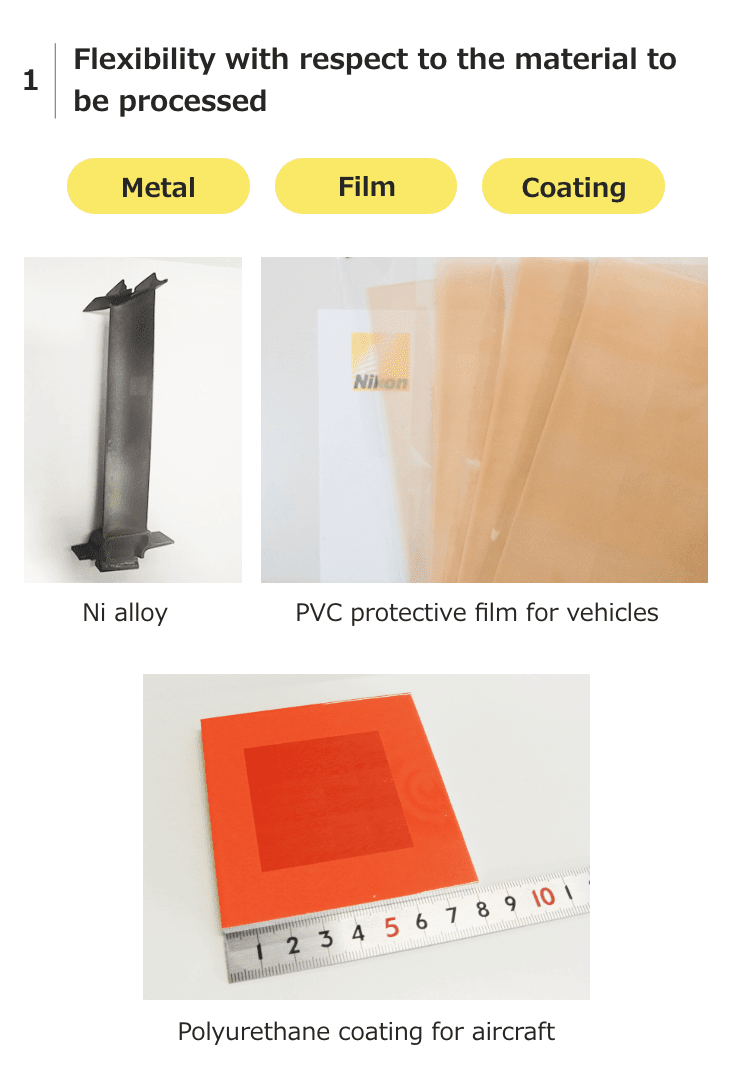
Riblets added to various materials
As described above, resin films were used for conventional riblets. However, while resin films had the advantage of being replaceable, they also had three limitations: heat resistance, durability and peeling. With Nikon’s laser processing, in addition to conventional film resins, riblets can be directly applied to materials including resins, metals and coatings. This makes it possible to use riblets in many ways including high-temperature environments where film would melt and strong currents where film would peel off.
Flexibility 2: Target shape
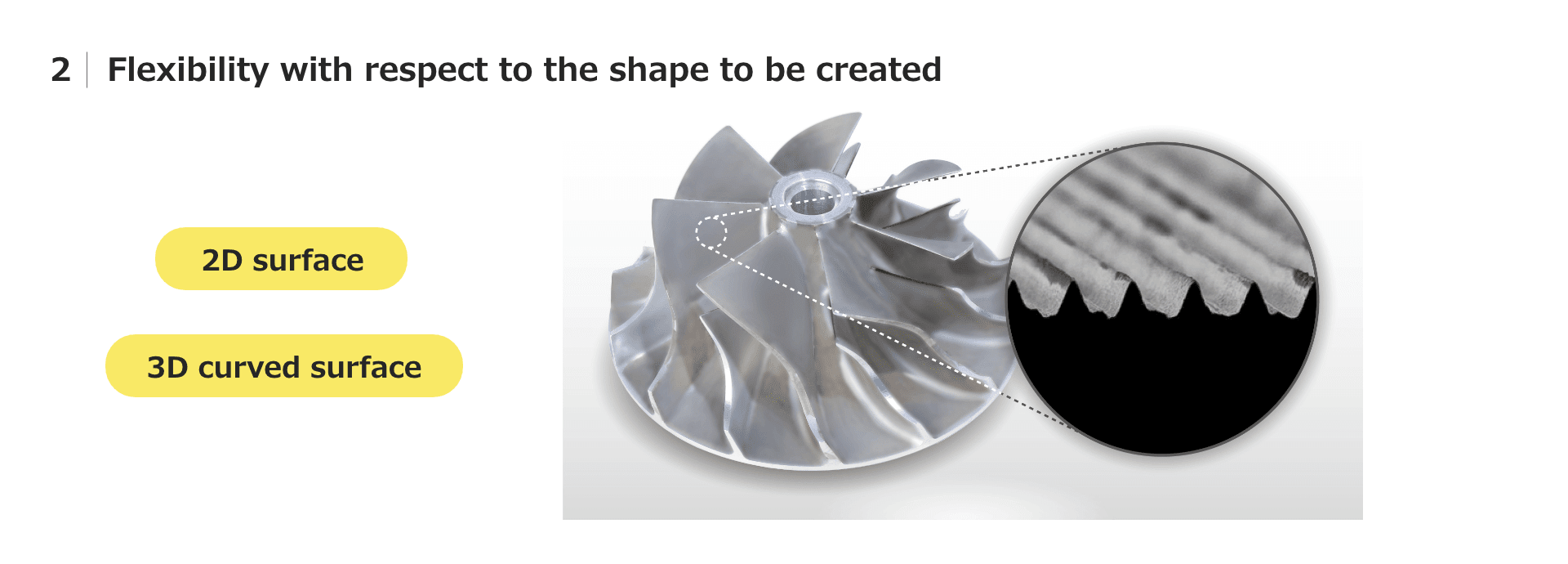
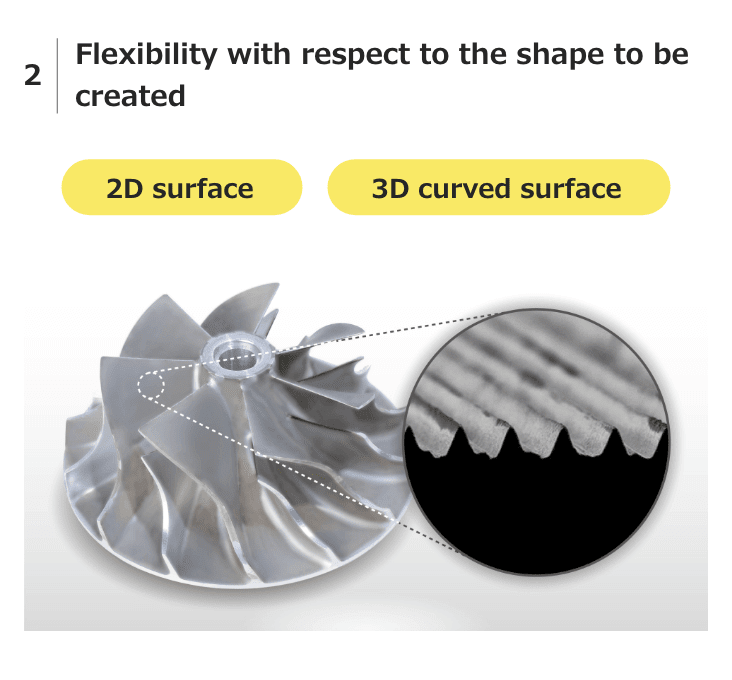
Conceptual diagram of riblet processing on a 3D curved surface
One feature is that riblets can be applied to a three-dimensional curved surface. Nikon can perform processing to directly apply riblets to three-dimensional curved surface, eliminating any concern of wrinkles when applying a film or the film coming off due to the curved surface. This makes it possible to more accurately apply the optimal riblet designed by analysis onto a product.
Flexibility 3: Design
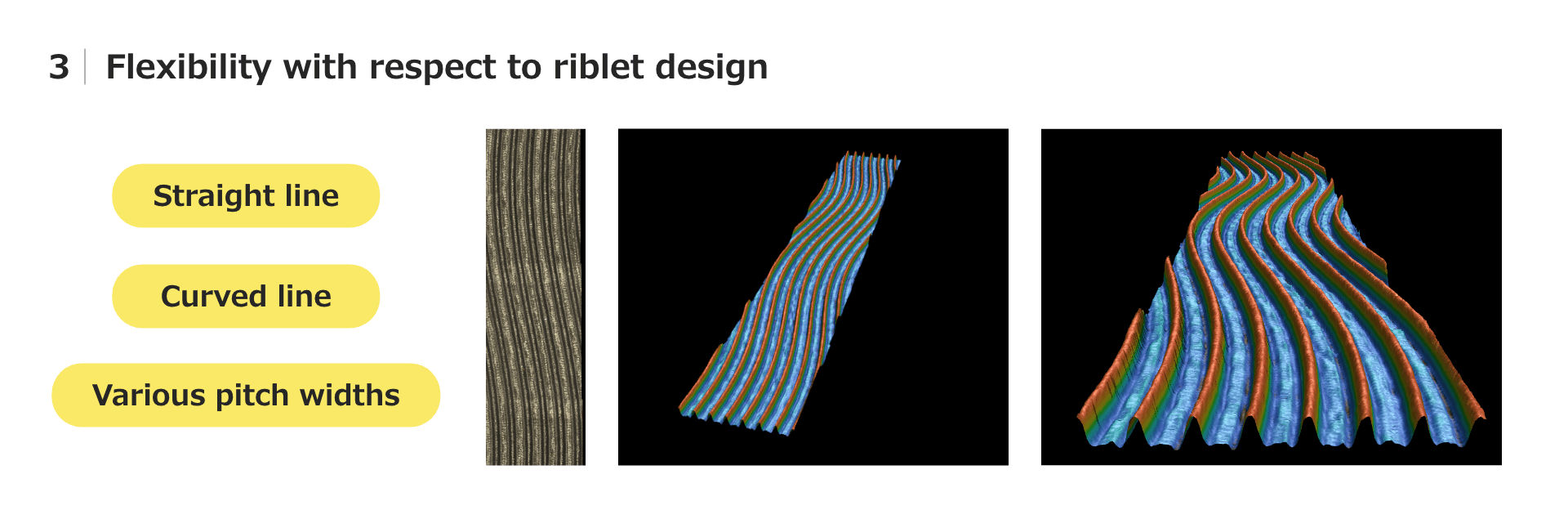
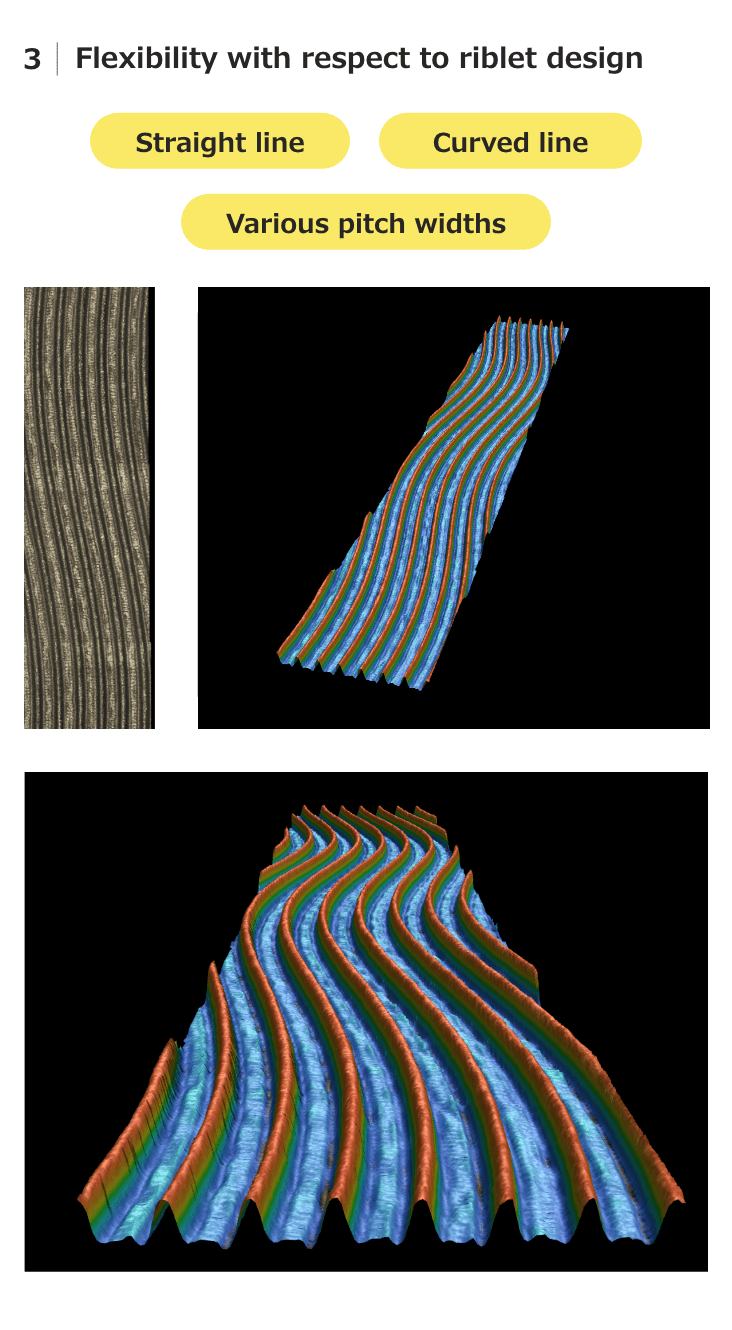
Riblets that create a smooth curve
As described above, it is important to use the optimal riblet shape for each part in order to maximize the riblet effect. However, with methods such as pattern embossing, due to model limitations it is not realistic from the perspective of cost and time to use more than a certain number of designs on a single product. Conversely, all designs used in laser processing are specified using software so it can be said that such design patterns are practically infinite. Having performed many riblet processing projects using a laser, Nikon has the knowhow to realize an infinite number of patterns with high precision.
Prospects for utilizing riblets
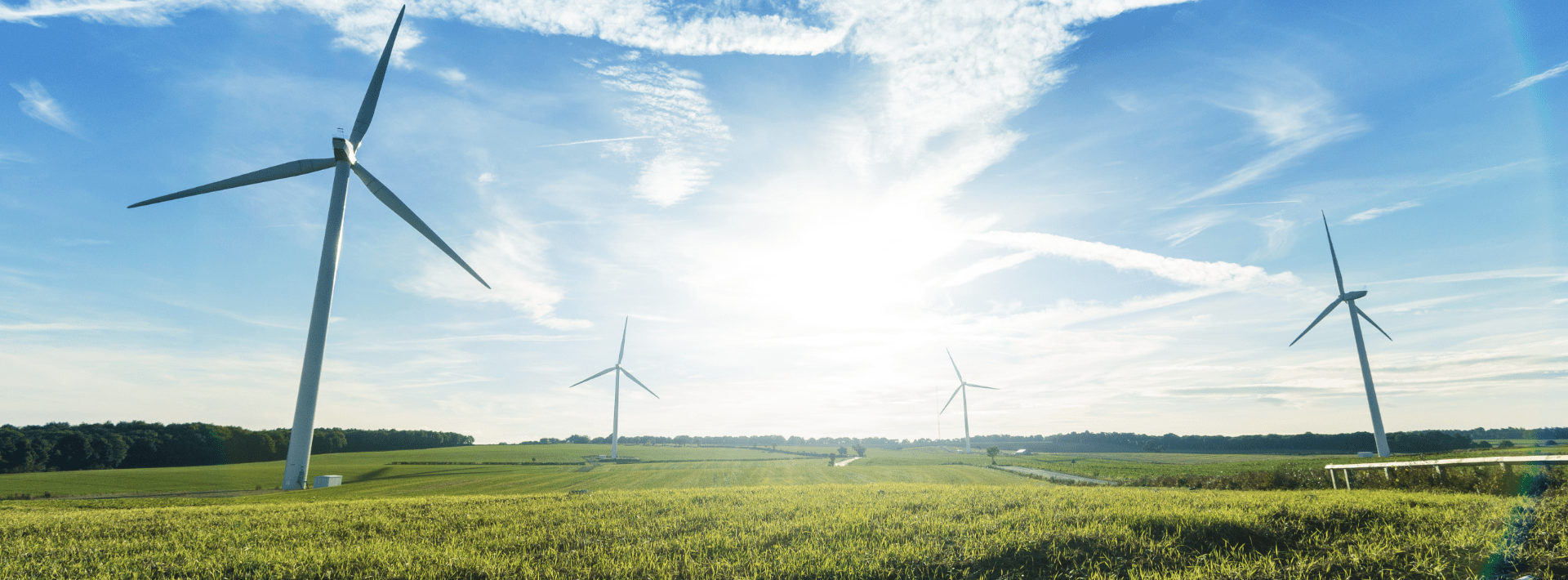
The range of riblets' applicability has expanded greatly. In addition to fields where application has already been examined such as aircraft, race cars and windmills, the range of potential application has now expanded greatly including gas turbines, propeller-driven aircraft, drones, pumps and home appliances etc. Together with partner companies that handle such products, Nikon provides a comprehensive service from preliminary prediction of effect to effect verification testing of customer products and mass production processing.