Flexible manufacturing using light
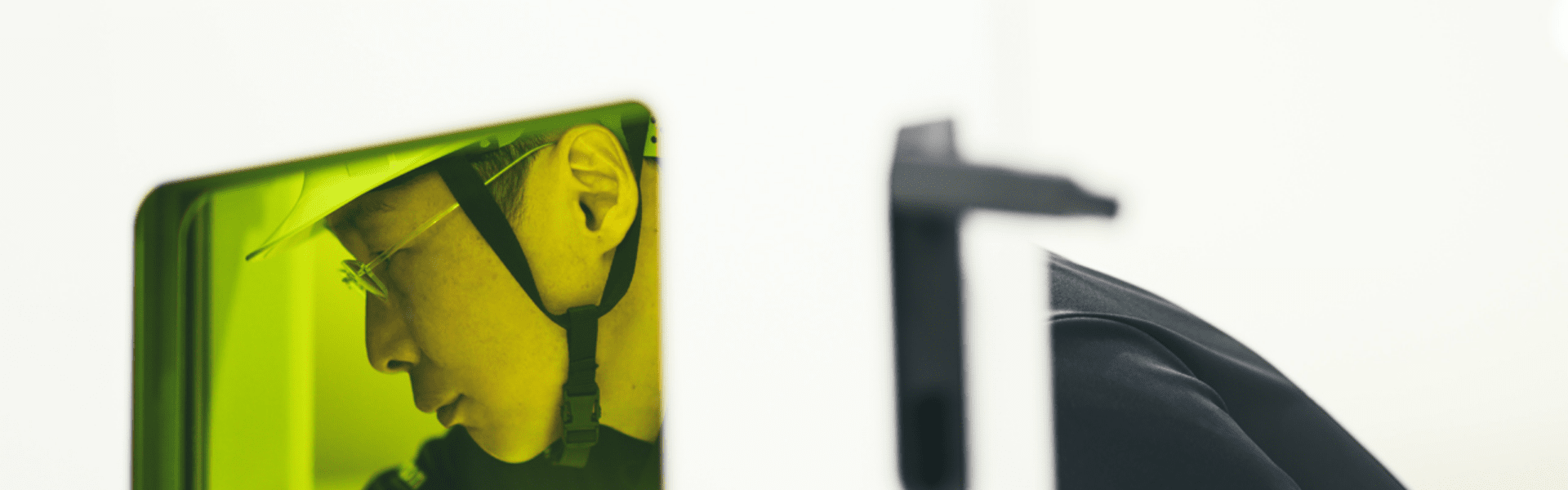
Nikon has realized additive manufacturing using a laser with the concept “using light to see and light as a tool”. This section explains the merits of Nikon’s metal 3D printer.
Metal additive manufacturing proposed by Nikon
Nikon’s metal 3D printer employs the laser metal deposition (LMD) method that builds up layers by melting the metal and depositing metal powder onto that part. A feature of this method is that additive manufacturing can be performed on existing parts. In addition to metal modeling from scratch, with its ability to perform tasks such as adding new functionality to existing parts and performing precise repairs, this machine expands the possibilities of metal modeling.
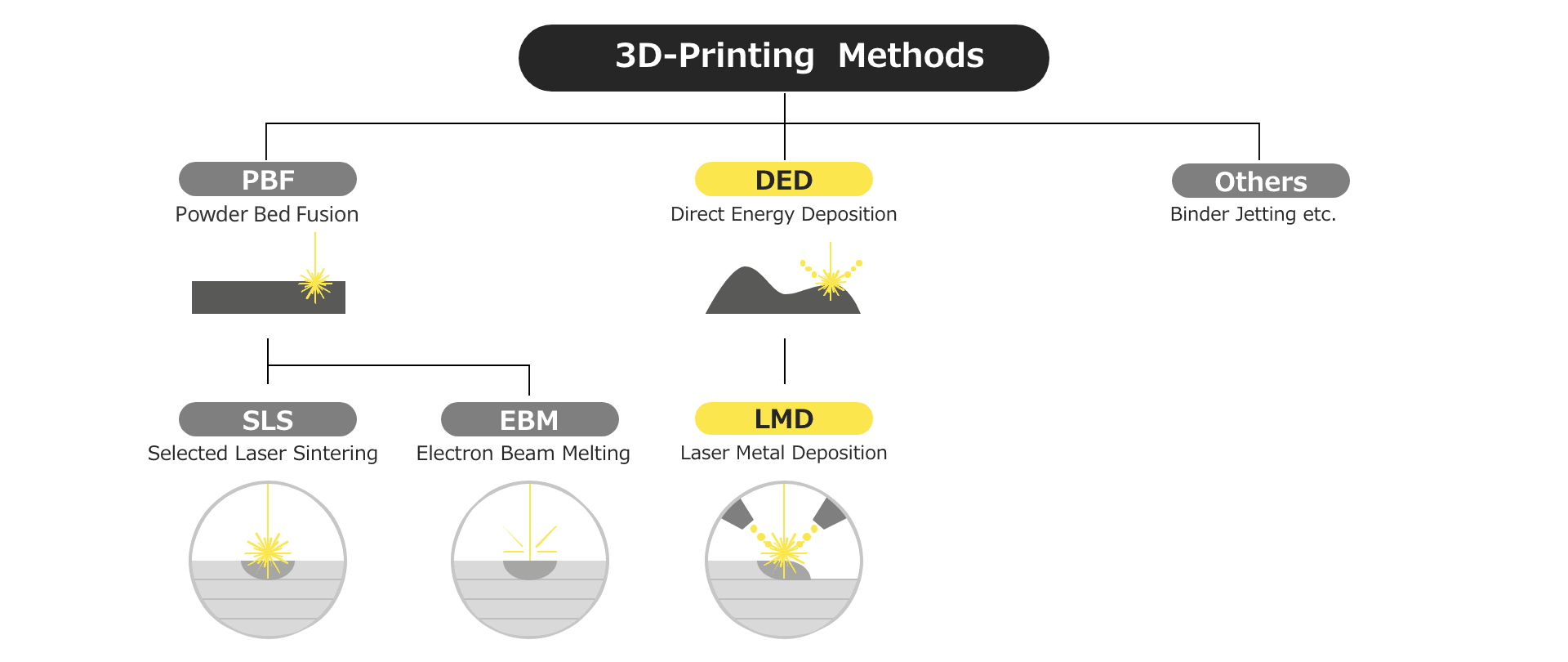
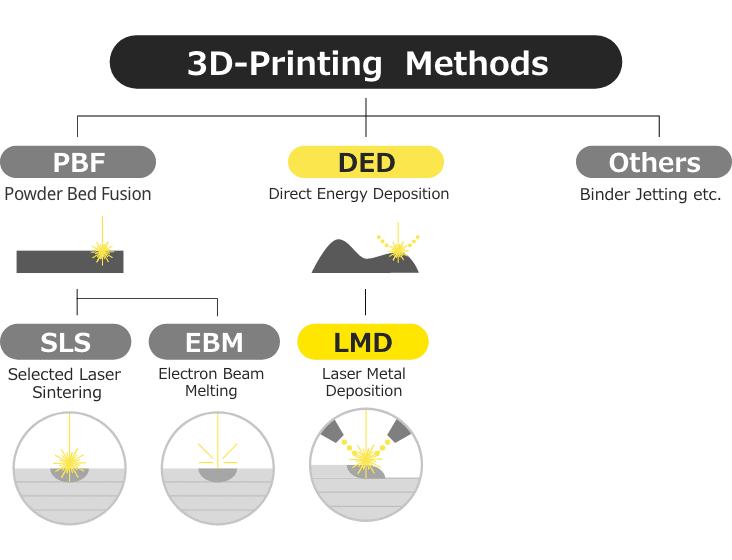
List of printing methods used by a metal 3D printer
Features additive manufacturing with a 5-axis mechanism
Nikon’s metal 3D printer employs a 5-axis mechanism. This 5-axis mechanism is composed of a 3-axis mechanism with the three axes X, Y and Z and a 2-axis rotation mechanism with an axis that rotates like a potter’s wheel and an axis that tilts like a swing. The 5-axis mechanism is employed to enable modeling with a high level of flexibility.
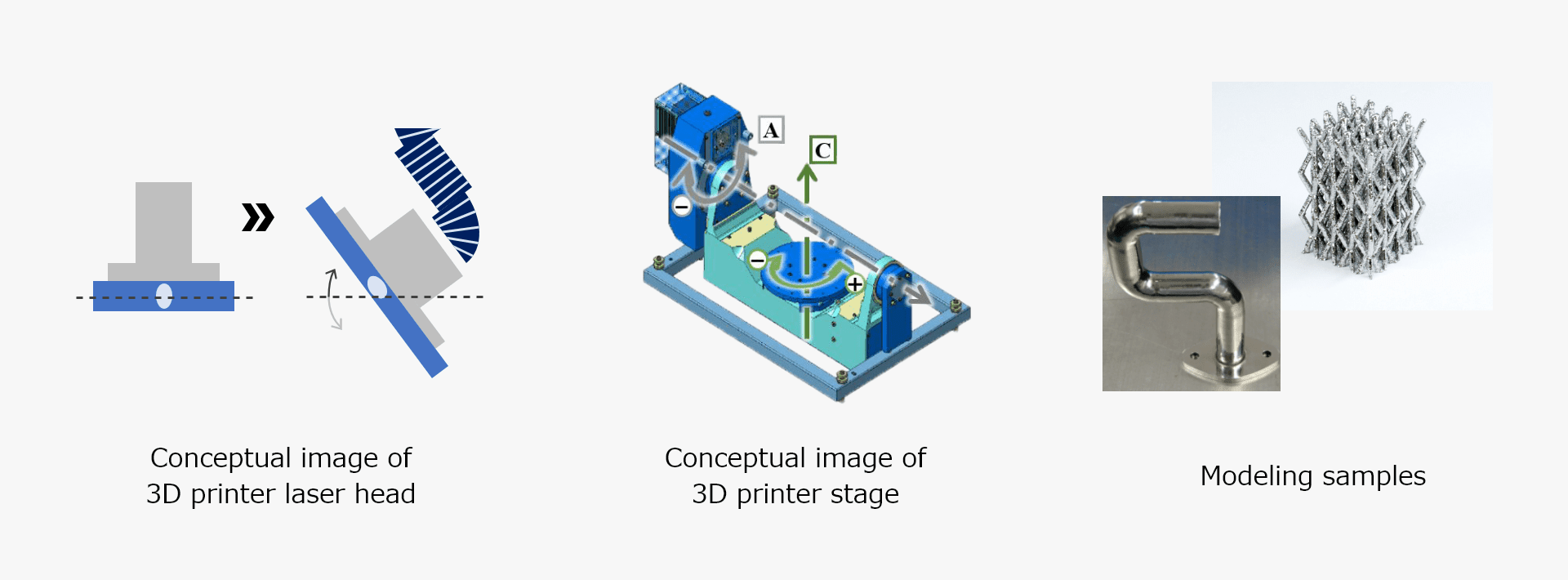
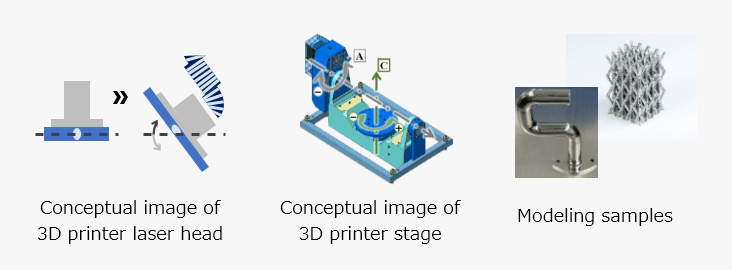
The image on the left shows modeling being performed with the stage swung to the side, and the image in the center shows stage rotation (C axis) and stage swing (A axis). This mechanism enables the creation of complex shapes like the one shown on the right.
Melt pool monitoring to realize uniform shapes
The state of melting in the metal melt pool is monitored and modeling operation is controlled to stabilize the modeling shape. This control achieves uniform shapes at edge areas where the heat dissipation differs, eliminating the generation of protrusions.
In addition, to improve modeling quality a powder supply feedback function is installed on the machine that observes the powder at high speed and controls the powder supply operation when powder is being supplied.
In addition, to improve modeling quality a powder supply feedback function is installed on the machine that observes the powder at high speed and controls the powder supply operation when powder is being supplied.

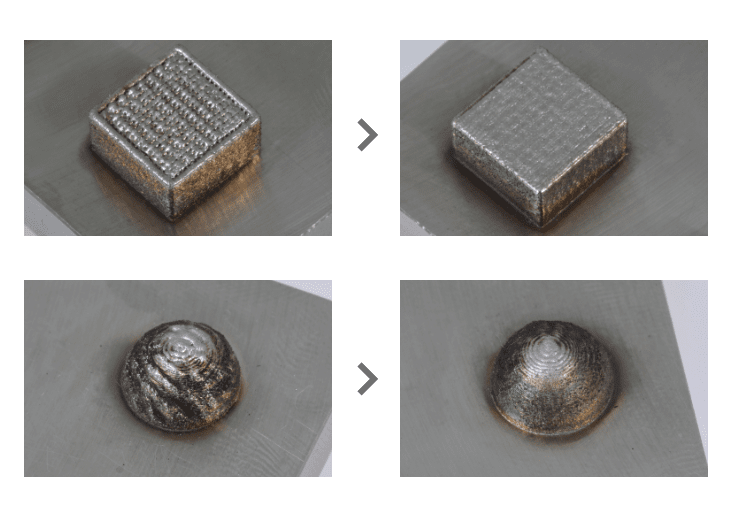
Comparison of modeling quality with/without melt pool monitoring
The modeling surface shown on the left with no melt pool monitoring is rough and uneven whereas with control by melt pool monitoring as shown on the right the top and peripheral parts of the modeling surface are stable and smooth modeling can be performed.
Broad range of usable materials means a wide range of needs can be met
Extremely versatile stainless steel, high speed steel usable as a material for tools capable of scraping metal at high speed, nickel-base alloys that are industrial materials with excellent corrosion and heat resistance, and titanium alloys that are used in various industries because they are light, strong and do not rust.
The ability to use these materials makes it possible to meet a wide range of needs in various industries including the machine processing, medical, and aerospace industries.
The ability to use these materials makes it possible to meet a wide range of needs in various industries including the machine processing, medical, and aerospace industries.

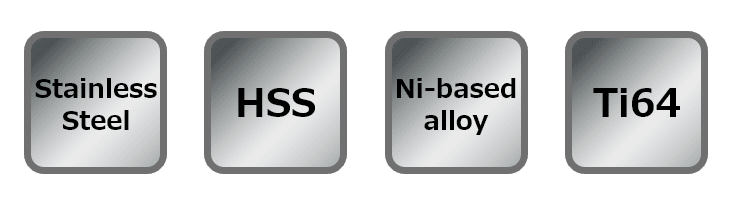
Materials that can be used with a metal 3D printer
Modeling quality and strength
The results of internal void inspection on an SUS 316L grade stainless steel 10 mm square cube modeled using standard modeling conditions is shown below. No voids (air bubbles, small cavities) are observed inside modeled object, indicating that it has no defects.
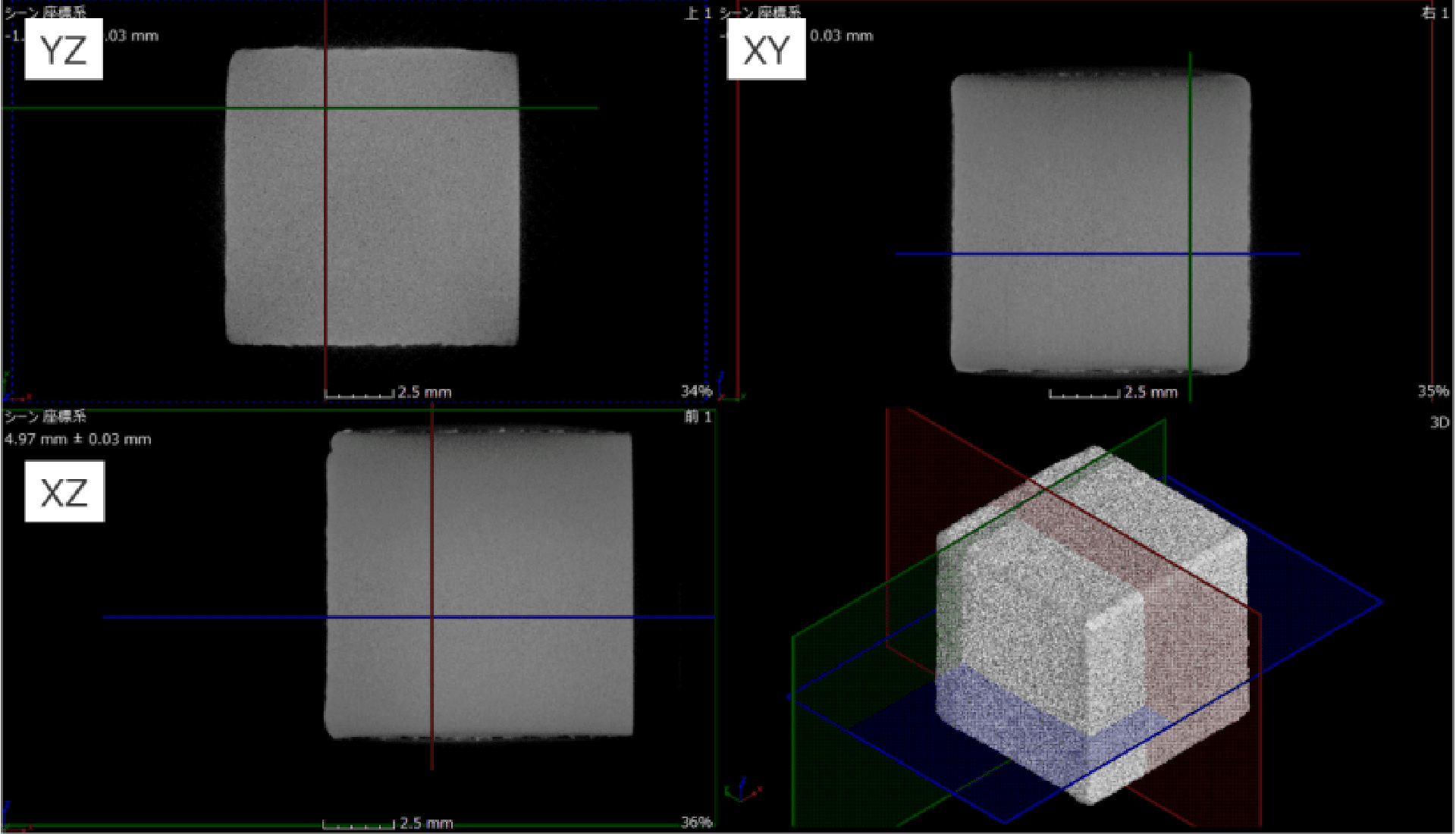
Results of internal void inspection using an X-ray CT inspection machine (Nikon XT H 320)
The following data shows the results of tensile strength testing that conforms to the JIS standard of objects modeled from SUS 316L grade stainless steel. Inspection is performed five times each for items modeled in the horizontal direction and items modeled in the vertical direction. As you can see, both guarantee strength that exceeds the reference value.
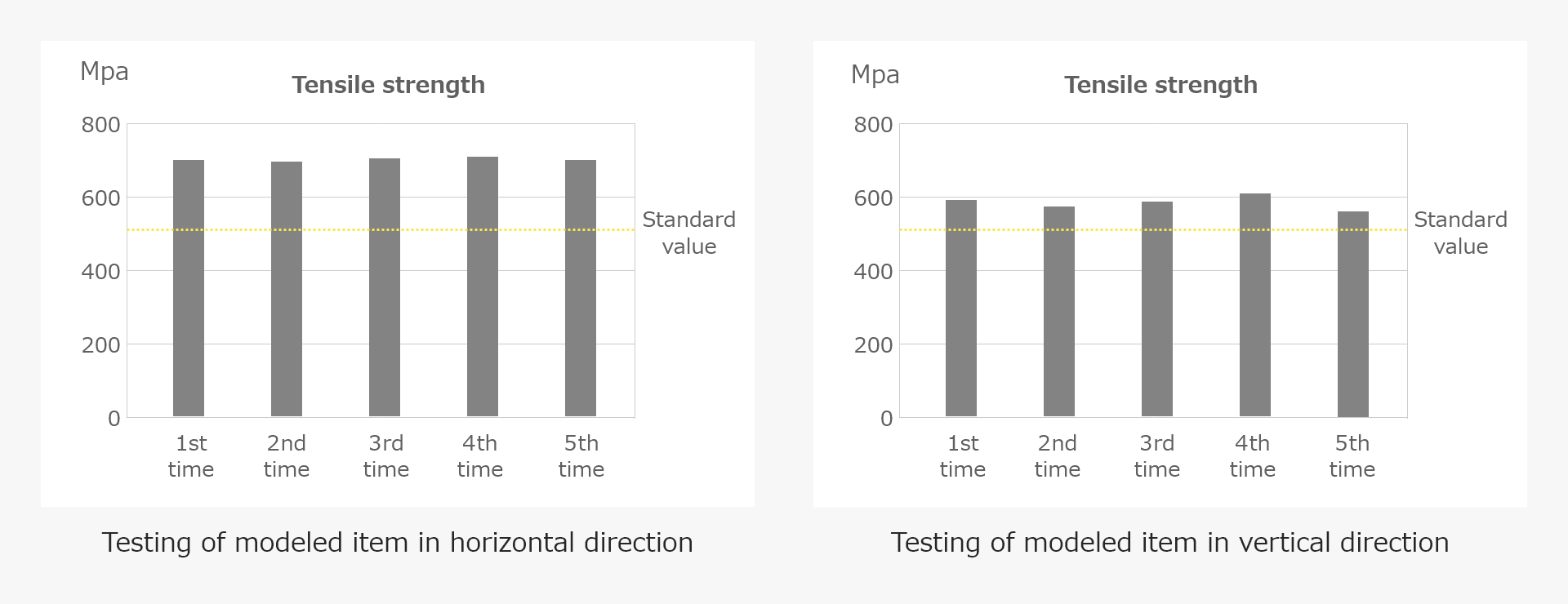
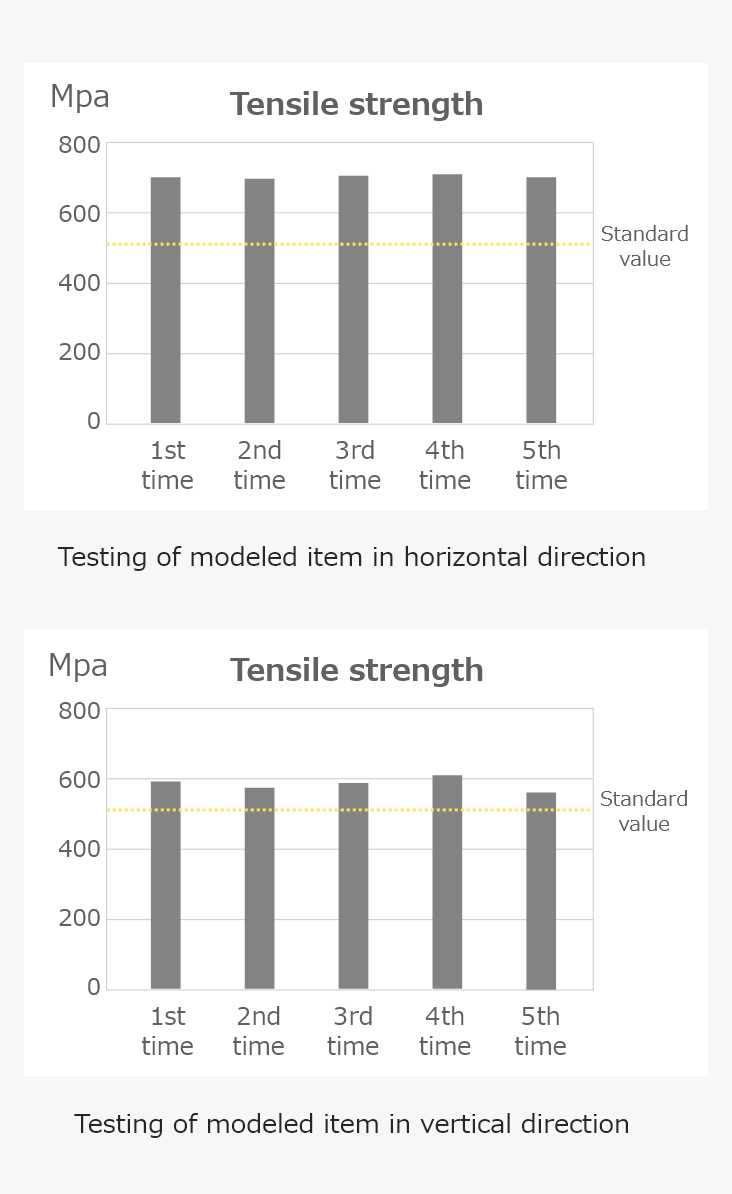
Tensile strength test results (in-house inspection)